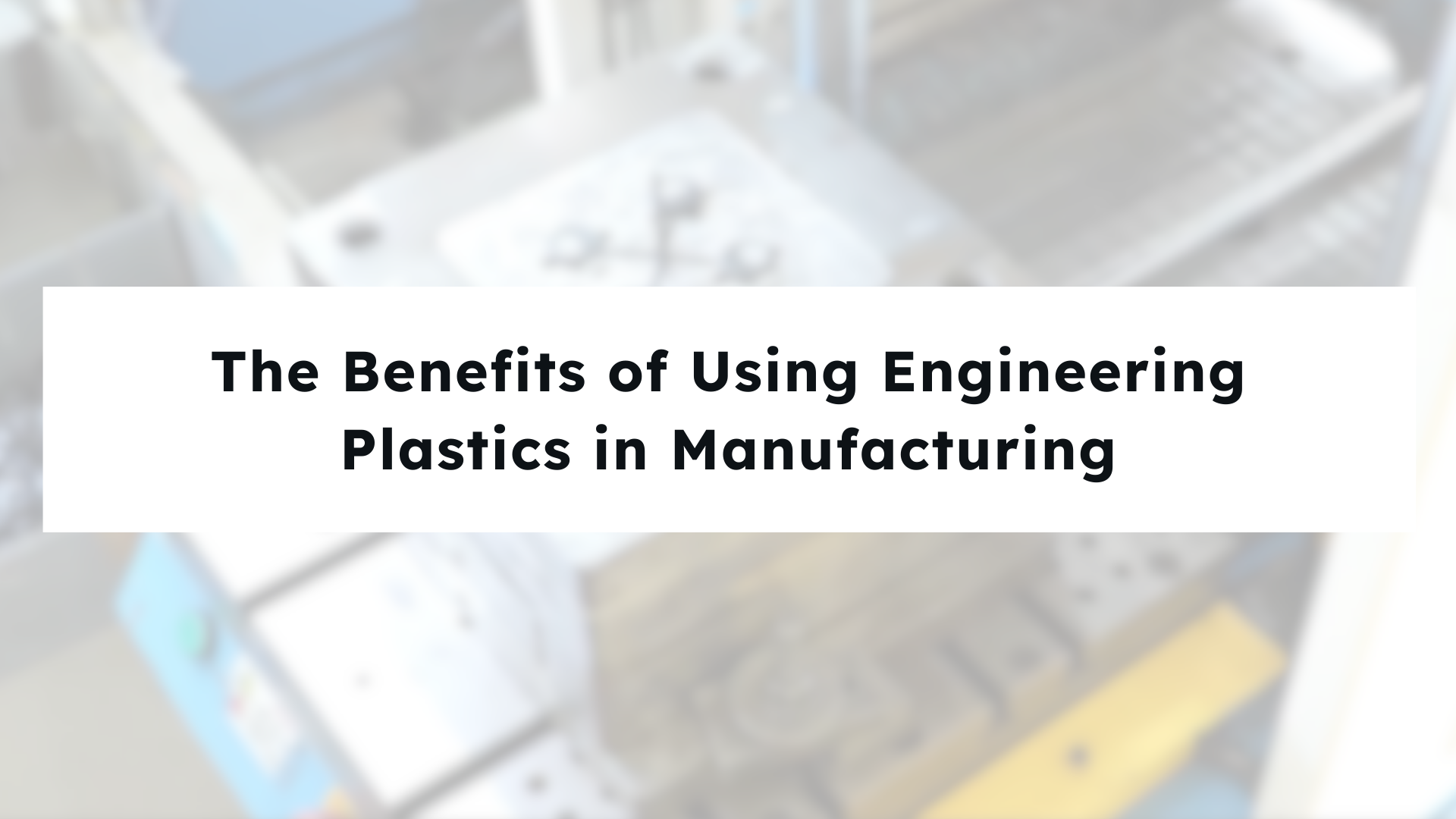
With a revolution in modern manufacturing, engineering plastics offer many more benefits than metals. Today, their versatility, strength, and efficiency have found many applications in almost all industries, from automotive to electronics. Let's closely look at why and how engineering plastics are applied.
Key Benefits of Engineering Plastics
Enhanced Durability and Strength
- These engineering plastics are designed to withstand high-stress environments and are ideal for components that must endure extreme conditions.
- They provide strength comparable to that of metals but are much lighter, enhancing the durability and effectiveness of the product. Plastic moulding manufacturers rely on these qualities to create long-lasting parts through plastic injection molding.
Lightweight and Cost-Efficient
- Engineering plastics are much lighter than metal. Therefore, they are ideal for the automotive and aerospace industries, where weight reduction is crucial.
- This decrease in weight reduces transportation costs and fuel consumption, further adding to overall cost efficiency.
- Plastic moulding manufacturers in India can achieve complex, lightweight designs with minimal material waste. Plastic injection molding allows for efficient production with reduced costs
Versatile in Design
- The flexibility of engineering plastics allows for custom designs, intricate shapes, and tight tolerances.
- Plastic injection molding generates complex geometries and smooth finishes, expanding design possibilities for plastic moulding manufacturers.
- These plastics can be tailored for heat resistance, electrical insulation, or chemical stability according to application needs, making them ideal for varied industries.
Chemical and Corrosion Resistance
- Engineering plastics are resistant to chemicals, moisture, and corrosion, making them ideal for medical devices, electronics, and chemical processing
- They withstand extreme conditions and do not corrode like metals, ensuring a longer lifespan
- Plastic moulding manufacturers in India utilize these properties to produce components that can endure oils, acids, and corrosive substances, hence increasing the reliability of the final product.
Conclusion
Engineering plastics are revolutionizing manufacturing with strength, versatility, and efficiency. With the assistance of Roots Polycraft, companies can experience top-quality, precisely molded components for various industry requirements. Advanced plastic injection molding techniques from Roots Polycraft provide reliable, sustainable solutions that help businesses enhance product performance, reduce costs, and stay competitive in today's evolving market.
Related Blogs
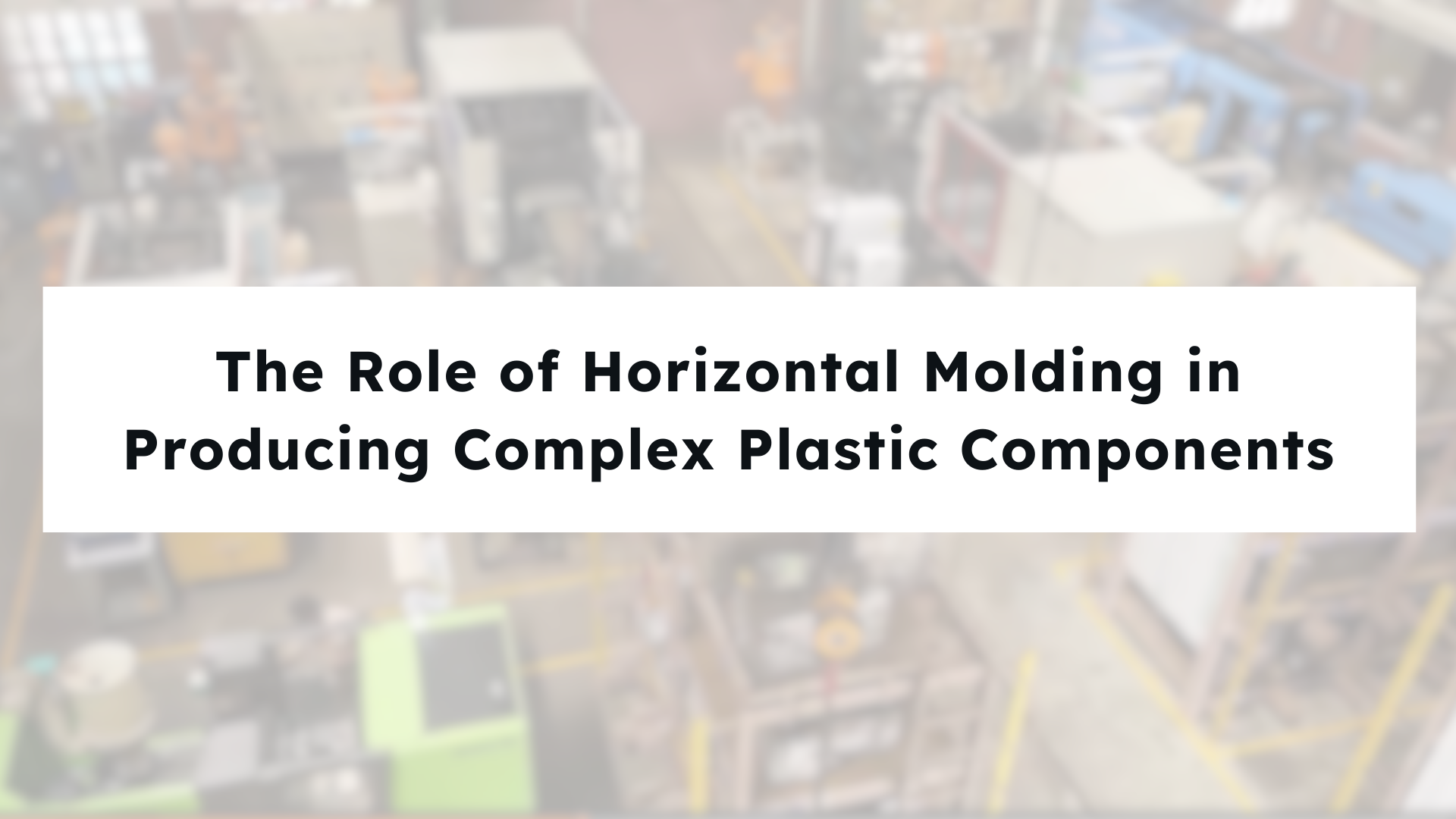
Horizontal injection molding is a versatile manufacturing process highly valued...
Read More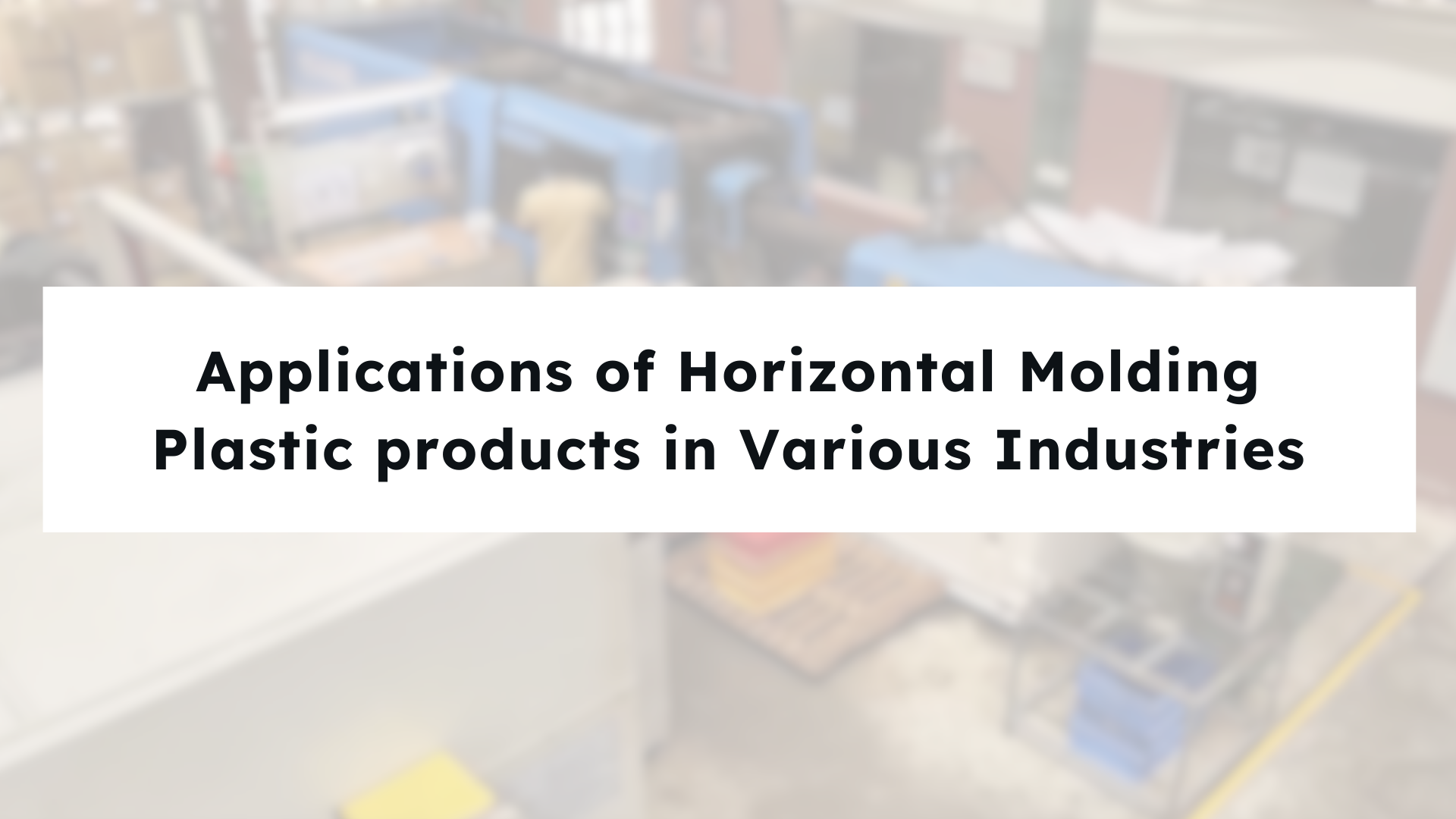
Horizontal injection molding is a standard manufacturing method that allows...
Read More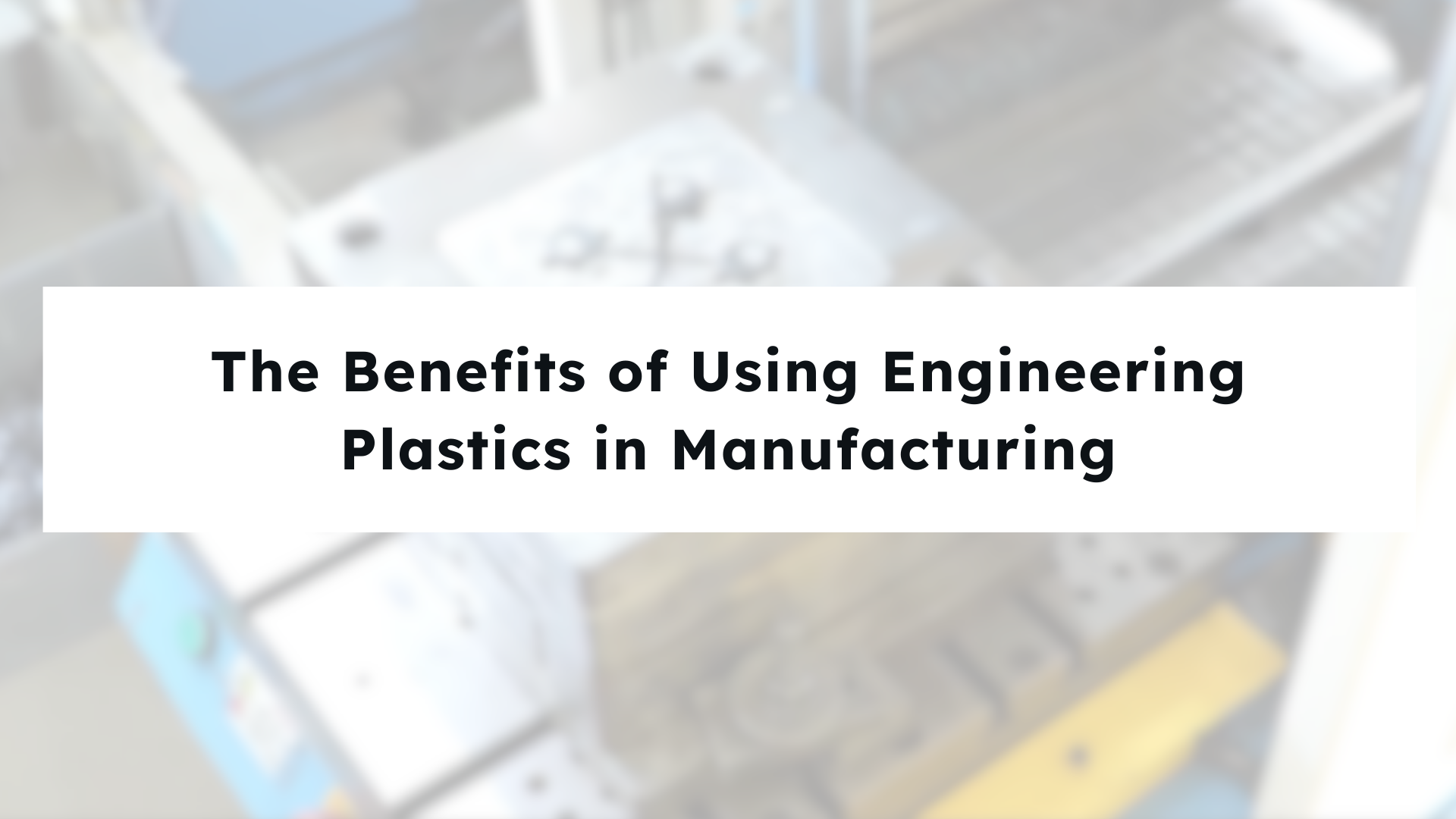
With a revolution in modern manufacturing, engineering plastics offer many...
Read More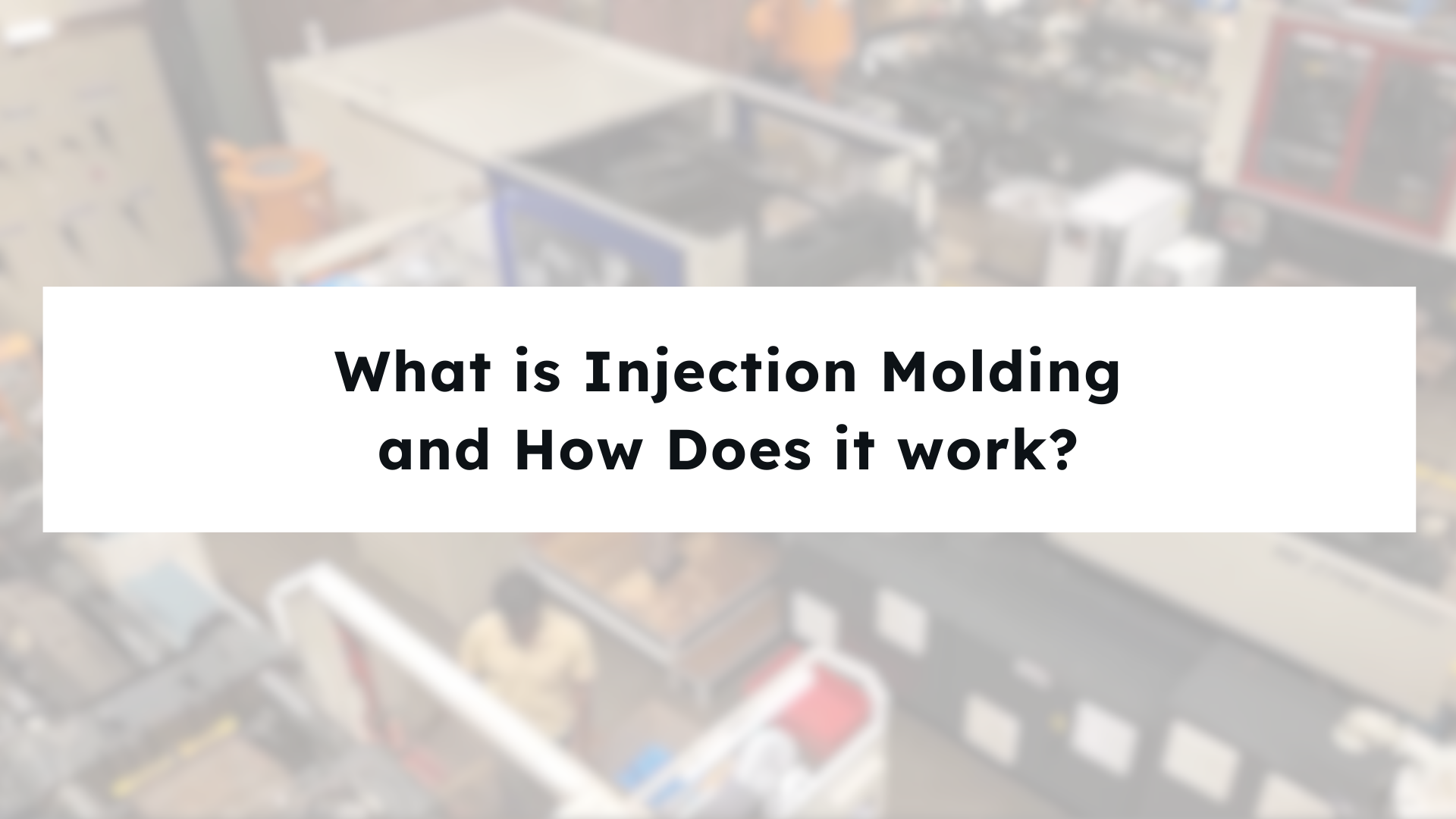
One of the most commonly used manufacturing processes to produce...
Read More